GKN Aerospace has partnered with North Carolina-based titanium developer IperionX to ship titanium plate take a look at parts manufactured with IperionX’s titanium angular powder and powder metallurgy methods.
Ranging from the profitable testing and validation of IperionX’s 100% recycled titanium powder comprised of GKN Aerospace’s scrap titanium feedstocks, this partnership primarily facilities on producing high-performance titanium plates for GKN Aerospace’s testing. At its conclusion, it leaves room for the potential for future collaboration between GKN Aerospace and IperionX, extending even to initiatives affiliated with the U.S. Division of Protection (DoD).
“GKN Aerospace is a frontrunner in sustainability and the precision manufacturing of titanium parts for the aerospace, area, and navy markets,” stated Taso Arima, CEO of IperionX. “We’re very proud to be working with GKN Aerospace to commercialize our market main high-performance and sustainable titanium merchandise.”

IperionX’s novel titanium manufacturing applied sciences
IperionX will make the most of its patented Hydrogen Sintering and Section Transformation (HSPT) applied sciences to boost the microstructure of titanium. This leads to improved energy and fatigue properties just like these present in conventional wrought titanium alloys.
The producer’s product line contains varied high-performance titanium powders and merchandise appropriate for the aerospace, protection, area, hydrogen, automotive, and client electronics sectors. This contains typical titanium plate, bar, and rod merchandise, in addition to high-performance ‘near-net form’ titanium parts geared toward enhancing sustainability and manufacturing effectivity.
Identified for its excessive strength-to-weight ratio and resistance to excessive temperatures and corrosion, titanium has been mass-produced utilizing the identical ‘Kroll Course of’ because the Forties. Nevertheless, this methodology is energy-intensive, expensive, and leads to important greenhouse gasoline emissions.
IperionX’s patented titanium manufacturing applied sciences supply a extra sustainable various, producing high-strength titanium merchandise with lowered vitality utilization and prices and 0 Scope 1 and a pair of emissions. With restricted home major titanium manufacturing capability within the U.S., which imports over 95% of its required titanium, IperionX seeks to reshore titanium mineral and metallic manufacturing, enhancing the availability chain with cost-effective, sustainable options.
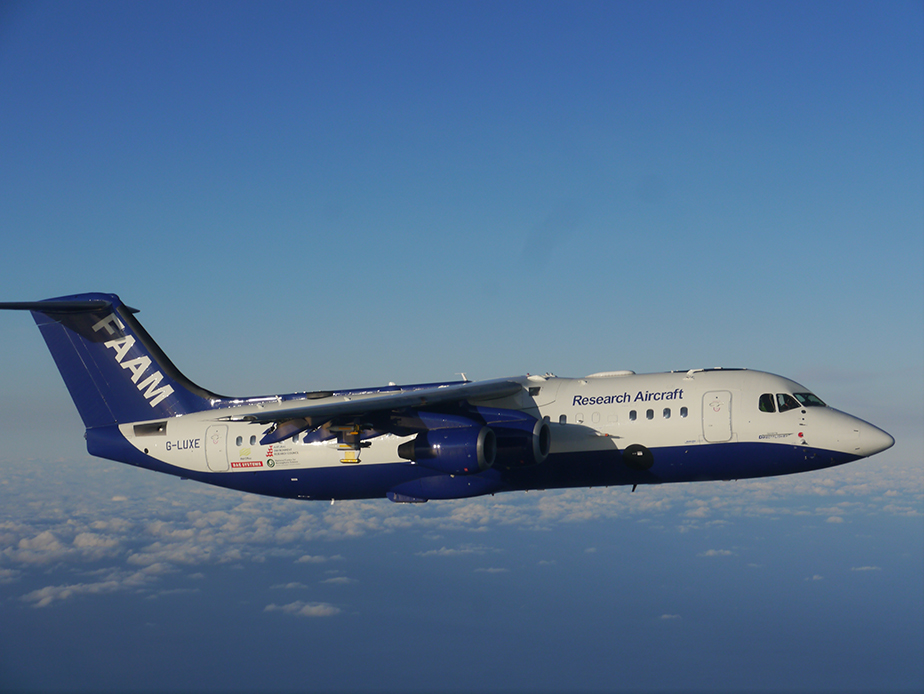
Sustainable titanium manufacturing
Researchers from RMIT College and the College of Sydney, in collaboration with Hong Kong Polytechnic College and Hexagon‘s Manufacturing Intelligence division, developed a brand new class of sturdy, ductile, and sustainable titanium alloys. These alloys supply the potential for inexpensive high-performance functions in aerospace, biomedical, chemical engineering, area, and vitality fields. The group built-in alloy and 3D printing course of design, utilizing Laser Directed Power Deposition (L-DED) to create these alloys. Lead researcher Professor Ma Qian emphasised the round financial system integration. These alloys could be crafted from waste supplies and lower-quality sources, with out the necessity for expensive components like vanadium and aluminum, relying as a substitute on considerable and inexpensive oxygen and iron.
IperionX offered multinational automotive producer Ford, with 100% recycled, low-carbon titanium. This alliance is according to Ford’s dedication to attaining carbon neutrality by 2050. The partnership concerned the design, testing, and 3D printing of titanium parts for future Ford Efficiency manufacturing automobiles. Moreover, IperionX’s titanium has the benefit of full recyclability on the finish of a product’s life, enhancing part sustainability. This contributes to the institution of a round, low-carbon automotive provide chain, an achievement not possible with different commercially out there titanium manufacturing strategies.
Who will win the 2023 3D Printing Business Awards? Make your nominations now!
What does the way forward for 3D printing for the subsequent ten years maintain?
What engineering challenges will should be tackled within the additive manufacturing sector within the coming decade?
To remain updated with the most recent 3D printing information, don’t neglect to subscribe to the 3D Printing Business publication or comply with us on Twitter, or like our web page on Fb.
Whilst you’re right here, why not subscribe to our Youtube channel? That includes dialogue, debriefs, video shorts, and webinar replays.
Are you in search of a job within the additive manufacturing business? Go to 3D Printing Jobs for a collection of roles within the business.
Featured picture reveals GKN’s Atmospheric Analysis Plane in-flight. Picture by way of GKN Aerospace.