German metallic AM firm LUMO has collaborated with Chinese language firm Eplus3D to create prototypes of compressor shafts for the development trade. These shafts, integral to screw compressors, facilitate gasoline compression between rotors and their housing. The required parts had dimensions of 100x100x400 mm and featured intricate freeform surfaces. Conventional manufacturing was deemed costly and time-intensive so the businesses turned to additive manufacturing.
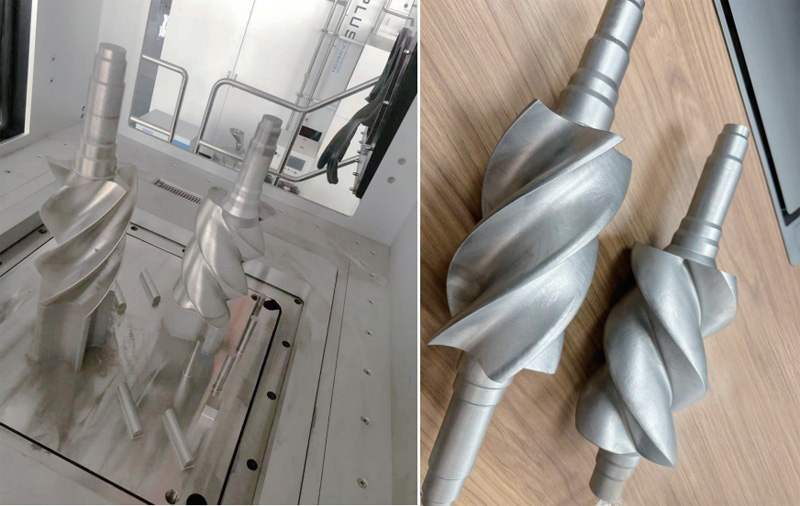
Screw compressors work by compressing air or gasoline utilizing two synchronized counter-rotating rotors. These rotors are linked by way of compressor shafts which endure demanding operational situations, necessitating sturdiness and resistance to moisture.
Evaluating manufacturing alternate options, casting was dismissed because of unsatisfactory materials properties and lead instances. CNC milling and grinding have been cost-prohibitive due to device put on and the parts’ complexity. 3D printing, particularly LBFB, stood out because of benefits like decreased lead instances, design flexibility, huge materials choices, and general value effectivity.
Eplus3D instructed their CX materials for its fascinating attributes like hardness and thermal conductivity. Following design changes, the 3D printing was executed utilizing powder mattress fusion expertise, guaranteeing precision.
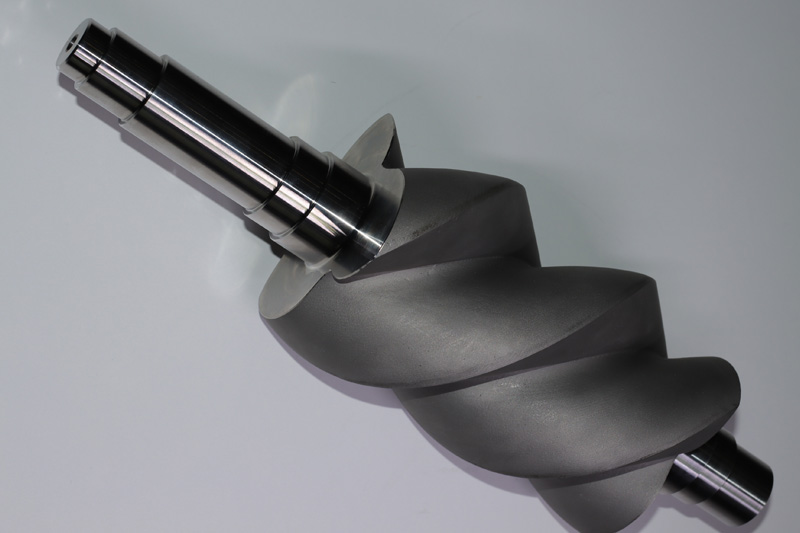
Publish-printing, the parts have been CNC machined, reaching a roughness of Rz 6.3 µm and exact bearing seats. Purposeful assessments validated the mechanical properties of those 3D printed shafts.
The partnership between LUMO and Eplus3D showcases the advantages of a focused collaboration between a 3D printing service supplier and an skilled system provider of additive manufacturing gear with broad experience throughout numerous industries.
Supply: metal-am.com
Come and tell us your ideas on our Fb, Twitter, and LinkedIn pages, and don’t overlook to join our weekly additive manufacturing publication to get all the most recent tales delivered proper to your inbox.