Austrian 3D printing firm M&H has built-in post-processing techniques producer Solukon’s SFM-AT1000-S depowdering system, to bolster the cleansing and post-processing of 3D printed metallic elements.
The SFM-AT1000-S is engineered to get rid of powder residues from intricate inner channels and cavities inside advanced elements. Giant and heavy metallic elements, reaching heights of as much as 1,000 mm and weighing a most of 800 kg, together with duties demanding excessive post-processing requirements, might be effectively cleared of powder residues utilizing this powder removing system.
“The SFM-AT1000-S, units new requirements within the manufacturing business – additionally because of its compatibility with our modern SPR-Pathfinder® software program. With this distinctive software program, particular person movement patterns might be calculated routinely for every part primarily based on the CAD file. By optimizing and automating their post-processing procedures, we provide our prospects – like M&H – a transparent aggressive benefit. With the Digital-Manufacturing unit-Instrument, a sensor and interface package, our companions even have most transparency over the depowdering course of,” mentioned, Andreas Hartmann, CEO and CTO of Solukon.
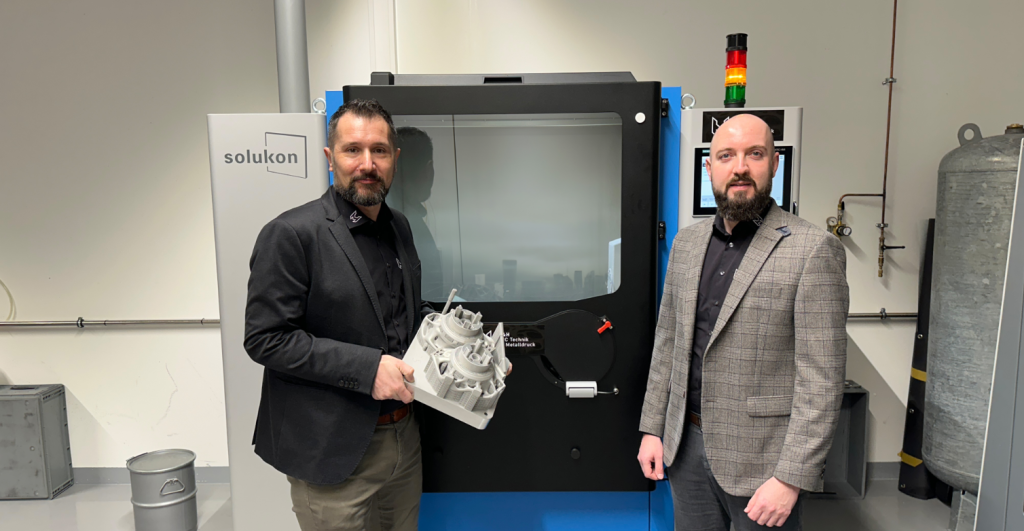
Cleansing advanced metallic elements with precision and security
The SFM-AT1000-S incorporates two rotating axes with servo drive know-how, facilitating exact motion alongside customizable paths. Moreover, it features a built-in high-frequency knocker designed to dislodge powder clumps, guaranteeing complete cleansing, even in confined channels. Notably, the system’s compatibility with reactive supplies allows inert gasoline inerting, guaranteeing adherence to security requirements.
M&H CEO, Patrick Herzig, explains the system’s precision as an important benefit, particularly in tackling the intricacies of advanced geometries. With its incorporation into its workflow, M&H goals to determine recent benchmarks in post-processing methods throughout a spectrum of supplies, starting from titanium and aluminum to stainless-steel, Scalmalloy, and Inconel.
M&H’s integration of the SFM-AT1000-S transcends normal practices, reaching into specialised sectors like aerospace and worldwide racing, notably Components 1. Herzig emphasizes the system’s pivotal position in assembly the rigorous calls for of those industries, stressing its precision and reliability. Moreover, when coupled with the just lately acquired SLM 800 3D metallic printer, M&H stands poised for large-scale manufacturing of advanced elements, positioning itself favorably within the aggressive panorama.
Solukon’s post-processing experience utilized in numerous sectors
Many corporations have been leveraging Solukon’s post-processing experience for his or her workflow. Collaborating carefully, CNC milling machines specialist Reichenbacher and Solukon improved the post-processing of 3D printed metallic elements by automating each unpacking and depowdering processes. This collaborative effort seamlessly built-in the removing of unfused powder from advanced constructions. The process commences with loading your complete container, housing the half, into the SFM-AT1000-S.Â
By rotational motion, free powder is emptied from the container, subsequently present process exterior preparation. Following this step, Solukon’s system harnesses Good Powder Recuperation (SPR) know-how to meticulously clear the half, using exact actions derived from the half’s CAD file. Able to dealing with containers weighing as much as 800 kg, the answer employs high-frequency vibration to successfully tackle difficult powder clumps nestled throughout the half’s inner channels.
A yr earlier than that, personal US aerospace agency Launcher chosen Solukon as its most well-liked provider for depowdering techniques, integrating SFM-AT1000-S for post-processing massive 3D printed rocket elements. Depowdering cooling channels and inner constructions proves advanced and time-consuming, significantly for copper elements susceptible to clogging.Â
Solukon’s techniques, pushed by SPR know-how, leverage adjustable two-axis rotation and focused vibration to take away extra powder routinely, enhancing effectivity, security, and high quality whereas minimizing prices. Launcher put in SFM-AT1000-S to utterly free rocket engines and combustion chambers from extra powder, addressing challenges within the post-processing of advanced metallic elements.
What 3D printing developments do the business leaders anticipate this yr?
What does the Way forward for 3D printing maintain for the subsequent 10 years?
To remain updated with the newest 3D printing information, don’t overlook to subscribe to the 3D Printing Trade e-newsletter or comply with us on Twitter, or like our web page on Fb.
Whilst you’re right here, why not subscribe to our Youtube channel? That includes dialogue, debriefs, video shorts, and webinar replays.
Are you on the lookout for a job within the additive manufacturing business? Go to 3D Printing Jobs for a number of roles within the business.
Featured picture reveals Patrick Herzig, CEO and Philipp Schwemberger, Head of Additive Manufacturing at M&H CNC-Technik. Picture by way of Solukon.